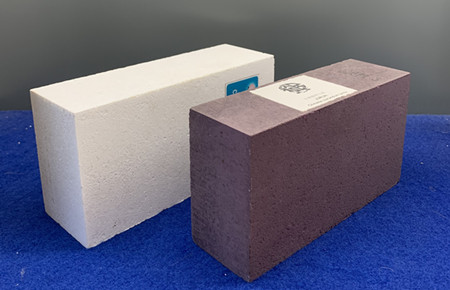
The property of chrome corundum bricks
The main ingredients of chrome corundum refractory brick are Al2O3 and Cr2O3, adding Cr2O3 to the Al2O3 single-phase refractory materials not only did not reduce the refractoriness of the materials, but the refractoriness increased with the increase of the Cr2O3 content.
Adding Cr2O3 to the corundum material, as the temperature rises, Al2O3 and Cr2O3 gradually form a solid solution, so that the corundum particles and the matrix are tightly combined, and further form a ring-shaped solid solution zone on the surface of the corundum particles, making the material tightly bond between particles and particles, particles and fine powder at high temperature, and the bonding phase is aluminum-chromium solid solution phase, which has a high melting point, and maintains bonding strength even at high temperatures. Therefore, chromium corundum refractory materials have strong mechanical properties at room temperature and high temperature.
Cr2O3 is a high-quality component in refractory materials, which can form high melting point compounds with a variety of oxides. For example, Cr2O3 and Al2O3 can form a continuous solid solution. The melting point of this solid solution is above 2050℃. Cr2O3 and MgO/FeO form high-melting magnesia-chromium spinel/chromium iron spinel. Cr2O3 and Cu2O can form compounds with a melting point above 1600℃.
In addition, Cr2O3 can also increase the viscosity of the slag, and the increase of the viscosity of the slag can slow down the penetration rate of the slag into the refractory. In summary, Cr2O3 can improve slag erosion resistance and anti-spalling properties.
Here below is the technical data sheet of chrome corundum bricks that Yumin manufactured:
The application of chrome corundum bricks
Because of its unique excellent properties, chromium corundum bricks serve a wide range of high-temperature fields with harsh use environments, including non-ferrous metallurgy furnaces, glass melting furnaces, garbage incinerators, etc. At the beginning of the development of chromium corundum, it was more widely used, and it was also involved in the fields of cement and steel metallurgy. However, due to the strengthening of people’s awareness of environmental protection, the voice for chromium-free in high-temperature industries is getting higher and higher, and alternative refractory products have been developed in many fields. However, this chromium corundum still exists in some furnace areas with harsh high-temperature use environments.
Because of its unique properties, chromium-containing refractories have been used in non-ferrous metallurgy industry kilns with a good application effect. Although many scholars are now studying chromium-free refractory materials in the field of non-ferrous metallurgy, So far, the use of chromium-containing refractories as the lining for smelting furnaces in the field of non-ferrous metallurgy is still the mainstream. At this stage, there are no better-performing materials to replace, except for chromium-containing refractories. In addition, copper converters and gas generators are also facing the same situation.
Aluminum-chromium-based refractories have better resistance to molten glass corrosion than normal corundum-based or aluminum-silicon-based refractories. Therefore, aluminum-chromium-based refractories are often used as refractory lining materials in key areas such as the serious erosion area of the target wall and the small furnace in the regenerator and the melting pool.
Among the refractory materials used for the lining of garbage melting incinerators, the refractories containing chromium oxide generally show good corrosion resistance. When the combustion temperature is higher than 1250°C, chromium corundum products will be used. The garbage melting incinerator generally has an oxidizing atmosphere, so C-SiC bricks with poor oxidation resistance cannot be used, and Al2O3-Cr2O3 materials and MgO-Cr2O3 materials are preferred.