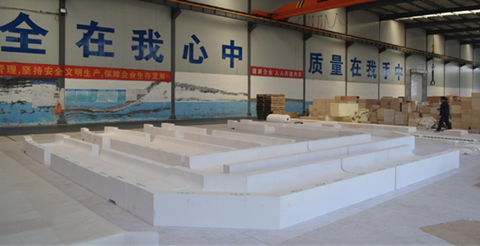
Refractory bricks refer to materials that can withstand high temperatures and can withstand the physical and chemical effects of high temperatures. In high-temperature furnaces or kilns, refractory bricks are the necessary lining materials. The selection of refractory materials is directly related to whether the entire kiln can work normally and the cost of its operation. When selecting the refractory bricks should not only consider their cost but also consider whether their performance meets the furnace operation requirements. If you also have doubts in this regard, you can refer to the following principles before selecting the refractory materials.
First of all, we must consider the refractoriness of refractory bricks. Refractoriness refers to the performance of refractory materials against high-temperature effects. Indicates the temperature at which the material softens to a certain degree. The refractoriness must be higher than the actual working temperature. For example, the refractoriness of fireclay bricks is 1730°C, and its use temperature is 1350°C.
Secondly, the high-temperature structural strength of refractories must be considered. Refractory materials will withstand a certain pressure when in use, and the structural strength of the refractories will change at high temperatures, so their high-temperature structural strength must be considered. This is characterized by its refractories under load, and the use temperature of refractories must be lower than its refractories under load. For example, the refractoriness of fire clay bricks is 1730°C, and its refractories under load is 1350°C, so the highest use temperature is only 1350°C.
Third, refractory bricks must have high thermal stability. There will be large temperature fluctuations in certain parts of the kiln. For example, when the furnace door is opened, cold air enters. The temperature of the furnace lining drops sharply. This requires refractory materials to have a certain degree of thermal stability to ensure normal operation.
Fourth, refractory bricks require high-temperature chemical stability. At high temperatures, the chemical properties of the refractory material may change and interact with the sample, furnace gas, etc., resulting in failure. So it is necessary to consider the chemical stability when selecting the refractory materials. For example, magnesia bricks can only be used as alkaline-slag resistant refractories, while silica bricks can only be used as refractories for acidic slag resistant.
Fifth, the bulk density of refractory bricks. When the refractories can meet the properties described above, it is better to choose materials with low bulk density to reduce heat storage, increase heat preservation effect, reduce furnace mass, and reduce energy consumption. Therefore, the current refractory materials mostly use lightweight refractory materials and new ceramic fibers that integrate heat preservation and fire resistance as refractory materials, which can greatly reduce costs.
Sixth, when it is used as an electric furnace lining, its conductivity must be considered, and must choose the refractory materials with insulating properties at high temperature for this kind of furnace.
The above are several important properties that should be considered when choosing refractory bricks for the furnace lining. All in all, the selection of refractory materials must ultimately follow two major principles: first, the performance of refractory materials must meet the production requirements, second, on the basis of the first, consider its economic requirements, and try to minimize the production cost.