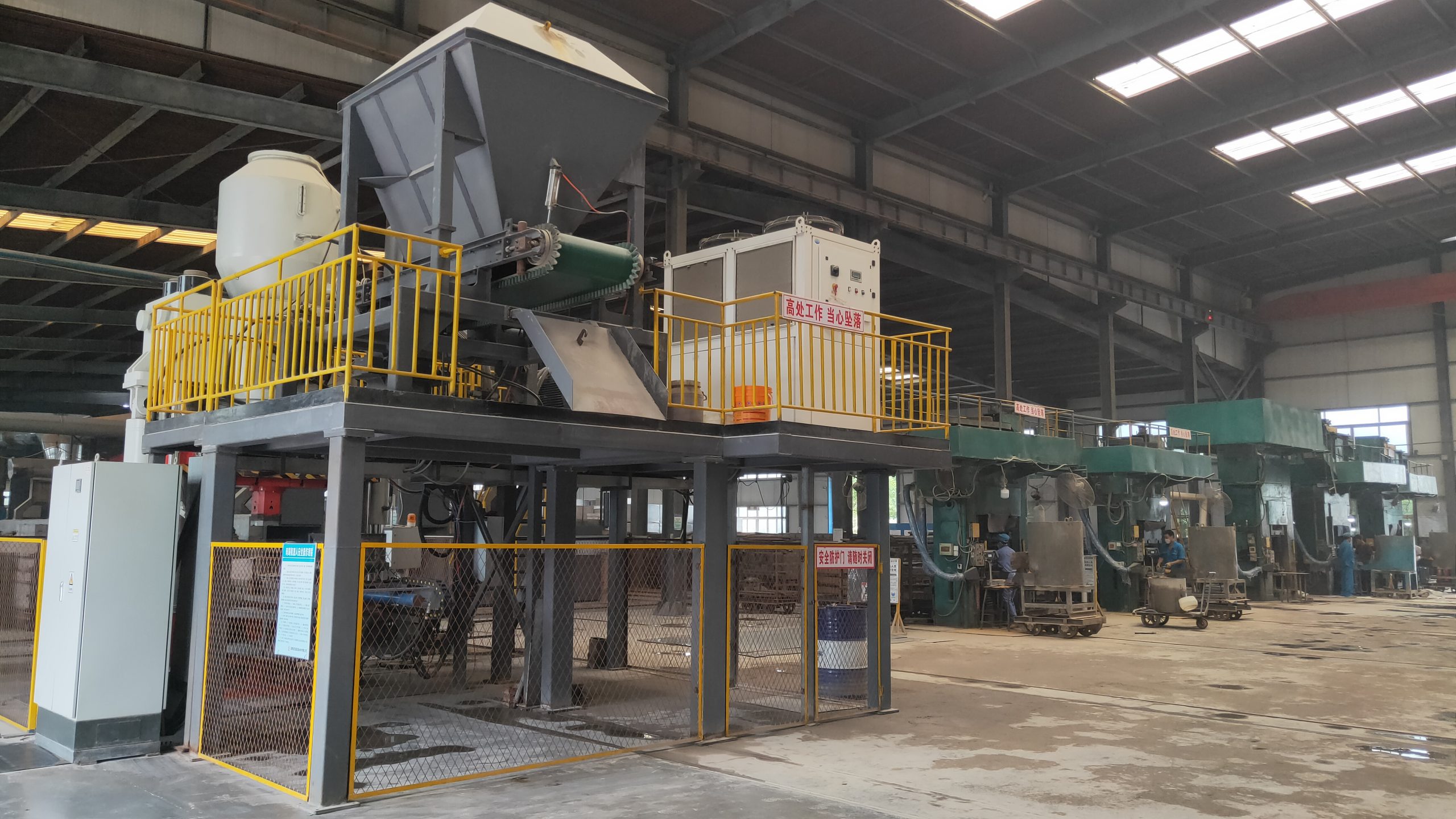
China had refractory manufacturing technology since ancient times, which was used in iron smelting, steelmaking, copper casting, ceramics, and glass production. Our country had made pottery 5000 years ago. Porcelain was made 2000 years ago, and the kiln and sagger used for firing are necessary for the refractory materials.
Before the liberation, the total production of refractory materials in the country was only 74,000 tons. The refractory materials needed for high-temperature industries, even the general refractory materials used in boilers, had to be imported from abroad. At that time, there were only a few small hand-made factories that could only make ordinary fire clay bricks, and the output was extremely low.
After the founding of the People’s Republic of China, the refractory industry developed rapidly in China, and modern factories were built, expanded, and upgraded throughout the country. A complete refractory manufacturing system with a large scale and high technical level has been formed. A number of new products such as high-alumina bricks and magnesia-aluminum bricks have been manufactured with Chinese resource characteristics, which has begun to change the monotonous situation of our country’s refractory product varieties. It was a symbol that the refractory industry has entered the ranks of national economic construction and development as an independent industry. There are already a large number of refractory manufacturers with modern equipment. Large-scale machinery and equipment for making refractory bricks can be made on their own, and modern factories can be designed by themselves as well, and scientific research on refractory materials has also been developed rapidly.
Our country has abundant resources of refractory materials. Magnesite, high alumina bauxite have large reserves and the quality is good. The raw materials of refractory clay, silica, and dolomite are widely distributed in China. The refractory raw materials such as serpentine, olivine, pyrophyllite, and zircon are also abundant. In addition, our country’s long coastline and inland lakes contain inexhaustible magnesia raw material resources.
China’s refractory manufacturing bases are mainly concentrated in Liaoning, Shanxi, Henan, and Shandong. Xinmi, Henan and Zibo, Shandong have developed into the main production areas of aluminum-silicon refractories, and Dalian, Liaoning, is the production base of magnesia refractories.
The basis for high-quality refractory materials is to choose high-quality refractory raw materials. In recent years, the manufacturers at home and abroad have higher demands for the quality of refractory raw materials, and a lot of research has been done in the aspects of beneficiation, purification, synthesis process, and calcination technology. The purity of raw materials is enhanced, the sintering process is improved, the composition structure is uniform, and the performance is stable, which provides a foundation for the development of high-quality, high-purity, and high-efficiency refractory products. The future development trend is to decrease the proportion of natural refractory raw materials, while the proportion of high-purity, high-density, and uniform quality refractory raw materials after beneficiation and synthesis continue to increase.