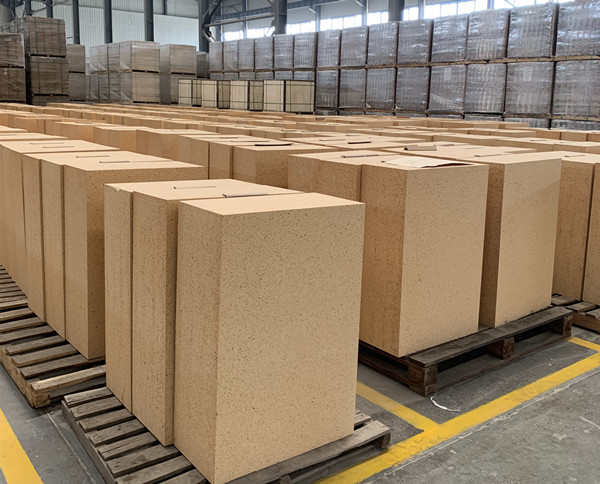
Here below to summarize the refractory materials used in the glass melting furnace:
1, Silica brick
The main component of silica brick is silicon dioxide (SiO2). The silica brick used in the glass melting furnace requires a SiO2 content of 94% or more, the maximum operating temperature is about 1600~1650℃, and the density is around 1.8~1.95g/cm3. The apparent porosity is required to be less than 22%. The larger the apparent porosity, the quality of silica brick is worse. It mainly used for crown and breast walls in the glass melting furnace.
2, Fused cast AZS brick
Generally, fused cast AZS brick( electro-fused zirconia corundum brick) is usually divided into 3 types based on the content of ZrO2: 33%, 36%, and 41%, The zirconia corundum bricks used in the glass furnace application contain 50%~70% Al2O3 and 20%~40% ZrO2. The bulk density is 3.4~4.0g/cm3, the apparent porosity is 1%~10%, and the maximum use temperature is about 1700℃. The fused cast AZS bricks with 33% and 36% ZrO2 content are normally suitable for the areas like melter side wall, breast wall, paving blocks, ports, and tongue, etc.
The fused cast AZS brick with content of 41% is used for melter’s bottom, melter side wall, throat, refiner side wall, refiner bottom, and other parts where are directly erosion by the glass liquid, this type is the most widely used fused cast refractory material in the glass furnace.
3, Fire clay refractory brick
The main composition of fire clay bricks is Al2O3. The content of Al2O3 is between 30% and 45%, the density is between 1.7 and 2.4g/cm3, and the apparent porosity is between 11% and 22%, the highest operating temperature is 1350~1520℃. In the glass industry, fire clay bricks are usually suitable for the areas like the bottom of the furnace, the side wall of the working poll, and the side wall, crown and bottom layers of the regenerator, and the chimney flue. When the temperature rises, the volume of fire clay bricks will also expand. When the temperature exceeds 1450℃, the volume will shrink again.
4, High alumina refractory bricks
The main composition of high alumina bricks is also Al2O3, but the content of Al2O3 should be greater than 46%, usually between 46% ~ 80%. The density of high alumina brick is 2.55~3.0g/cm3, the apparent porosity is about 18%~24%, and the maximum operating temperature is 1500~1650℃. When the apparent porosity of the high alumina brick is low, the corrosion resistance property is better. High-alumina bricks can be used for side wall of cooling cool, regenerator crown, and regenerator walls.