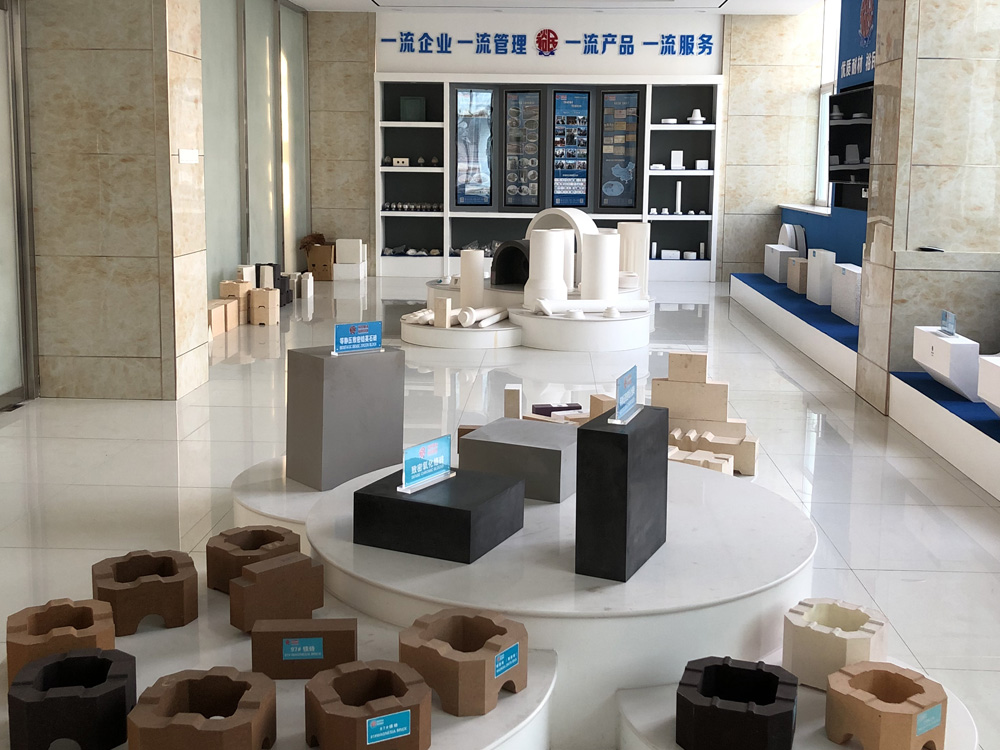
The main composition of mullite refractory bricks is Al2O3, the content of Al2O3, is around 75%, because it is mainly mullite crystal, so we call it mullite brick. The density is 2.2-3.2g/cm3, the apparent porosity is 1%-12%, and the maximum operating temperature is 1500~1700℃. Sintered mullite is mainly used for side walls of regenerators. Fused mullite is mainly used side wall of cooling poll, observation holes, wall stacks, etc.
6, Fused corundum bricks
It mainly refers to fused-cast corundum refractory bricks, mainly containing 92%~94% Al2O3 corundum crystal phase, its bulk density is 2.9~3.05g/cm3, and the apparent porosity is between 1%~10%, the highest operating temperature is about 1700°C.
Fused alumina has excellent resistance to glass dialysis and hardly pollutes molten glass. It is widely used for the side wall of the working poll, bottom pavings, forehearth, throat, wall of feeder in the glass melting furnace, etc., which are in contact with glass liquid and require no pollution to the glass liquid.
7, Alkaline refractory materials
Alkaline refractory materials mainly refer to magnesia bricks, aluminum magnesia bricks, magnesia chrome bricks, and forsterite bricks. Its unique property is excellent corrosion resistance to alkaline materials, and its refractoriness is 1900~2000℃. It is widely used in the upper wall of the regenerator of the glass melting furnace, the regenerator wall, the checker of the regenerator, and the partial structure of the port.
8, Insulation refractory products
the heat dissipation area of the glass melting furnace is large and the thermal efficiency is low, so in order to save energy and reduce consumption, a large amount of insulation materials are required for comprehensive heat preservation. In particular, the side wall, bottom, crown, and wall in the regenerator, melter, working end, etc. must be insulated to reduce heat dissipation. The apparent porosity of insulation brick is very large, weight is light, and the bulk density not exceeding 1.3g/cm3. Because the heat transfer performance of air is very poor, the thermal insulation brick with a large apparent porosity has a thermal insulation effect. Its thermal conductivity is 2 to 3 times lower than that of general refractory materials, so the greater the apparent porosity, the better the insulation effect. There are many different types of insulation bricks, including fire clay insulation bricks, silicon insulation bricks, high alumina thermal insulation bricks, and so on.
9, Unshaped refractories: ramming materials, castable, and mortars