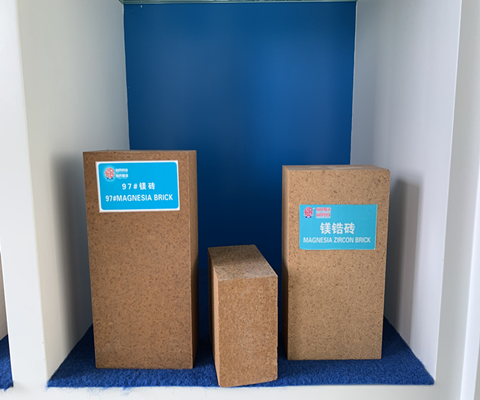
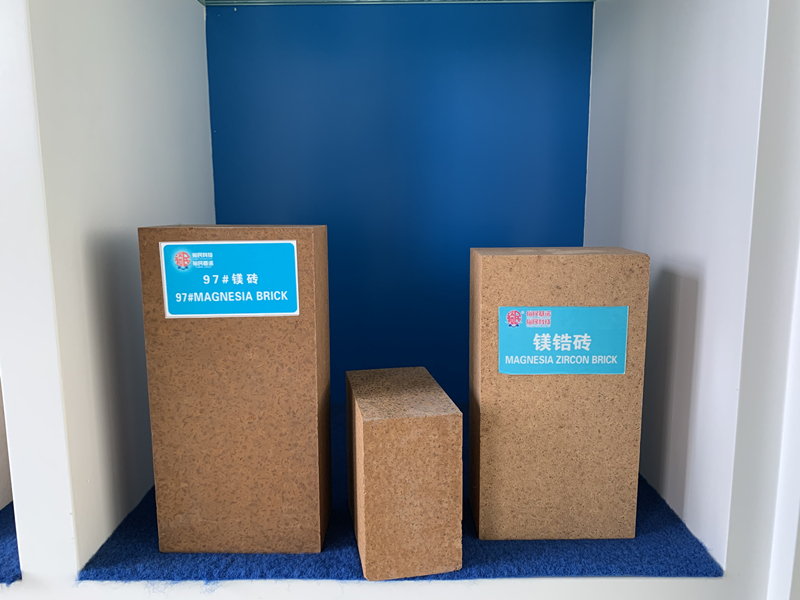
The important way to improve the refractory brick quality is to increase the purity of the refractories, reduce the number of low melts and increase the density and high temperature strength of the product. High density magnesite refractories and high purity direct bonded magnesia refractories are the trends in the development of magnesia refractories in China and abroad in recent years.
1, High purity raw materials, high pressure forming, high temperature sintering
A basic principle in refractory production is based on refined materials, that is, high purity. The fluxing agent impurity content has much influence on the slag resistance and high temperature strength of furnace lining bricks.
The purpose of high pressure forming is to improve the strength and density of the refractory product. The higher the density of the brick, the more difficult it is for the slag to penetrate into the brick.
High-temperature sintering is a measure to achieve full sintering on the basis of high-purity raw materials. This can form a so-called direct bonding structure in the brick under the condition of little liquid phase, and at the same time increase the density of the product and increase the high temperature strength of the brick. It should be said that the increase in the high temperature strength of the brick is due to the comprehensive results brought about by factors such as reduced impurity content, high pressure forming and high temperature firing.
2, Control the composition of refractory bricks
- Control C/S ratio
The smaller the ratio of CaO/SiO2 is, the secondary phase co-existing with the main crystalline phase periclase in the magnesia refractory material is mainly the presence of low-melting minerals such as forsterite. It is also necessary to increase the CaO/SiO2 ratio from the perspective of slag resistance because magnesia bricks with a higher CaO/SiO2 ratio have better corrosion resistance to the initial slag.
- Reduce the flux function of B2O3.
3, Adjust the mineral composition of the refractory product, increase the initial temperature of the liquid phase and reduce the amount of liquid phase at high temperatures.
The use of high-purity refractory raw materials, high-pressure molding, and high-temperature firing can obviously improve the quality of refractory materials, but this often leads to cost constraints. In terms of improving quality, a meaningful method is to understand the role of low-melting substances, so as to control them and reduce their harmful effects. This can be done from two aspects: avoiding the generation of eutectic, that is, increasing the initial temperature of liquid phase generation and reducing the amount of liquid phase at high temperatures; controlling the distribution of the liquid phase so that the liquid phase does not surround the refractory solid particles at high temperatures. And repelled in the inter-particle gap. In this way, the liquid phase will not penetrate the particles, so that the contact between the solid phase particles increases, that is, the so-called direct bonding.
4, Control the structure of refractories
The so-called structure control is the phase distribution in refractories.
In conclusion:
- For magnesia bricks containing MgO and liquid phase at high temperature, in order to increase the degree of direct bonding between periclase, or to prevent the liquid phase from penetrating the periclase particle boundary, it is very great to add Cr2O3;
- For materials with two solid phases and liquid phases (Dolomite bricks, magnesia chrome bricks, or chrome magnesia bricks) at high temperatures, the combination of different particles is easier than the combination of the same particles. Therefore, it is very advantageous to use spinel or M2S, C2S high melting point minerals as the secondary relatively direct bond.
The second conclusion has general significance, that is, it is also applicable to corundum bricks and mullite-based high-alumina refractories.