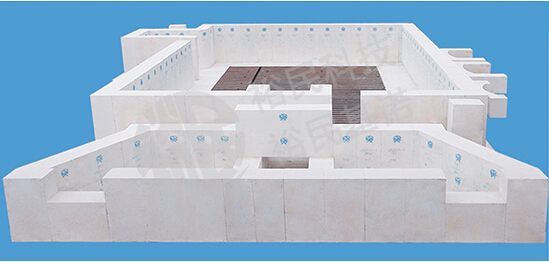
1, The refractory bricks used for the sidewall:
Currently, the melter side wall mainly uses fused cast AZS refractory bricks,
As for the refractory brick used for sidewall, it is required to be highly resistant to corrosion, not to cause any defects (such as stripes, stones, bubbles) to the molten glass, not to color the molten glass, and to have a certain degree of thermal shock resistance and low thermal conductivity. The ideal sidewall bricks are fused cast AZS refractory brick, and there are 3 types ( AZS-33, AZS-36, AZS-41 )of Fused cast AZS which are determined by the content of zirconia. The sidewall of the melting zone usually uses AZS-41, and the side wall of the cooling zone uses AZS-33.
2, The refractory bricks used for the bottom:
The conditions for the bottom refractory bricks are the areas where the temperature of the molten glass is lower and the flow is weaker. The bottom bricks are required to be wear-resistant and have totality. Nowadays, the multi-layer composite bottom structure is mostly used. Generally, a protective layer is built under the bottom bricks ( large-shaped fireclay bricks are used ), and zirconia ramming materials or fused zircon-corundum ramming materials are laid on the top of the large-shaped fireclay bricks, the fused zircon-corundum ramming material is better. This layer of ramming material and the bottom of the pool are sintered into a whole, requiring no shrinkage, no expansion, no cracks, and very dense, which prevents the leakage of glass liquid to the greatest extent and forms a strong bottom structure with sufficient strength.
The paving bricks are in direct contact with the glass liquid, which can well protect the ramming material bottom. The fused AZS bricks with good corrosion resistance and wear resistance are commonly used (high-quality sintered AZS bricks are also workable). The advantages of the composite pool bottom structure are: reducing heat loss, prolonging the life cycle of the pool bottom, and improving the quality of the molten glass.
3, The refractory bricks used for the doghouse:
The doghouse bricks are affected by the erosion of powder and glass liquid, material layer wear, scouring of liquid flow, and flame. Especially the doghouse corner bricks, the protruding part of the corner suffers strong abrasion and erosion, and the temperature differences of the inner and outer surfaces of the bricks are relatively large, and cause high mechanical stress, in addition, the area has a certain temperature fluctuation, so it is easy to be damaged. It is regarded as one of the weakest parts of the glass kiln, and necessary to use high-temperature, wear-resistant and corrosion-resistant refractory materials, commonly uses void free fused zirconia corundum bricks containing 41% of Zr2O3, and increase the thickness of the bricks to enhance air cooling. except for corner bricks, other parts can use ordinary fused cast AZS-33 bricks, chrome refractory bricks and zircon mullite bricks.
4, The refractory bricks for the cooling zone:
The condition of the cooling zone is that the melted liquid glass enters the later stage of the melting process, and it must not cause any defects to the molten glass (including stones, streaks, and bubbles). Since the temperature of the molten glass in this zone is lower than that of the melting zone, so the erosion damage to the bricks is lighter. The cooling zone requires AZS-33 brick, AZS resintered bricks and sintered zircon mullite bricks.