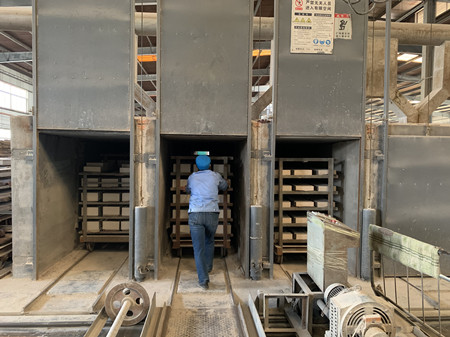
1.The selection and processing of raw materials for refractory materials
1, Refractory raw material selection
From a chemical point of view, all elements and compounds with a high melting point can be used as raw materials for refractory materials; from a mineralogical point of view, all high refractoriness minerals can be used as raw materials for refractory materials. With the development of modern industry, the use of high-purity raw materials is a pre-condition for the manufacture of high-quality refractory materials.
It is especially important to strictly control the quality of raw materials, due to there are a wide variety of raw materials, a wide range of sources, and a large number of demands for refractory materials. In the process of purchasing raw materials, the purchasing department and the quality department are responsible for the evaluation of the supplier’s product quality and supply capacity, Qualification certificates, reputation and other inspections.
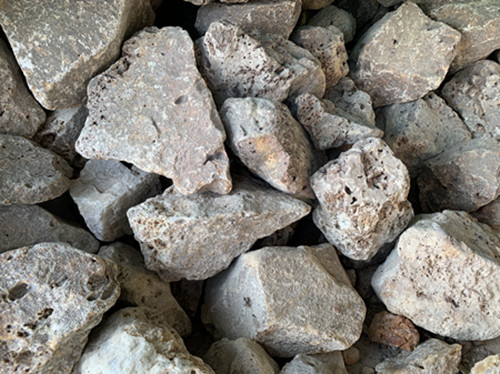
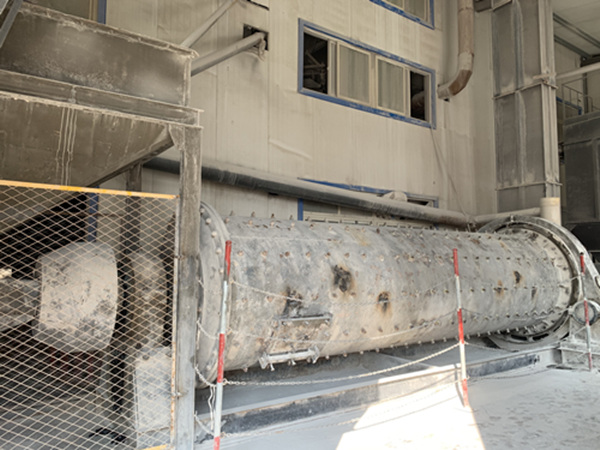
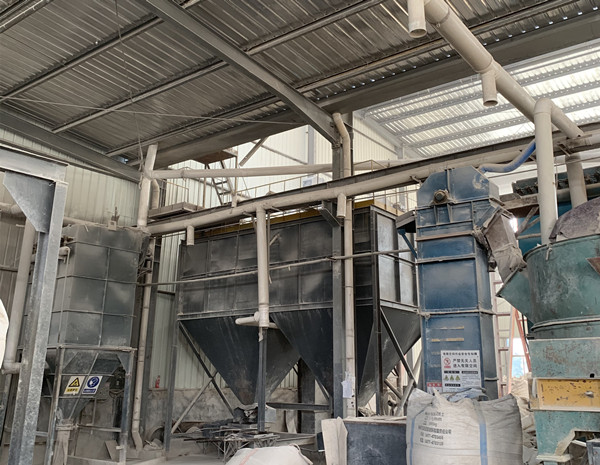
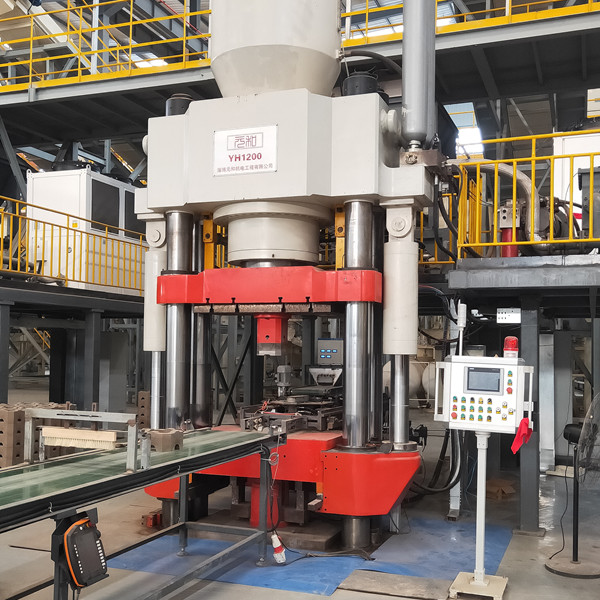

The semi-dry method-the water content of the billet is about 5%;
Plasticity method-the water content of the billet is about 15%;
Grouting method-the water content of the blank is about 40%
Semi-dry forming is the most common method for the general refractory products, As for what specific forming method will be used, it mainly depends on the nature of the billets, the shape and dimension of the refractory product, and the technical requirements. The common forming methods are as follows:
- Semi-dry pressing
- Grouting method
- Plastic forming method
- Vibration forming method
- Hot pressing method
- Hot die casting (hot pressure grouting)
- Electro-fused casting method for fused AZS
- Isostatic pressing method
4. The drying process of refractory materials
The purpose of drying is to improve the mechanical strength and ensure that the firing can proceed smoothly in the early stage. The semi-finished products after forming generally need to go through the drying process before firing. if the moisture content of the bricks is too high before entering the kiln. it is easy to generate cracks in the firming process. The strength of the dried bricks is greatly improved, which can reduce the damage rate during transportation and kiln loading.
The drying process can be divided into three stages:
The first stage is the constant speed drying stage, the most important stage in the drying process, this stage discharges a large amount of water, in the whole stage, the drainage rate is always constant.
The second stage is the reduced-speed drying stage. With the normal drying time or the decrease of the water content of the embryo body, the effective evaporation area on the surface of the embryo body gradually decreases, and the drying speed gradually decreases.
In the third stage, the drying speed is gradually approaching zero until the moisture of the embryo body stops decreasing.
The obvious degree of the above three stages depends on the amount of water in the embryo body. Generally, the three stages are more obvious for the embryo body formed by the plastic method, but for the embryo body formed by the semi-dry method with little moisture, such as Multi-clinker bricks, silica bricks, magnesia bricks, etc., are not obvious.
5. The firing process of refractory materials:
Firing is the last process in the production of refractory materials. The product undergoes a series of physical and chemical changes during the firing process. Under the action of high temperature, the embryo body reduces its porosity, increases its density and strength, forms a high-temperature stable crystal phase, and produces volume changes, so that the embryo body becomes a certain size, shape and structural strength of refractory product. According to product characteristics, it is necessary to formulate a reasonable firing system. Generally divided into four stages,
Pre-heating
Firing
Warming
Cooling
The firing equipment has down-draft kiln and tunnel kiln. At present, tunnel kilns are the main firing equipment, but the inverted flame kiln still has a certain use-value for refractory products with small production volumes or special shapes.