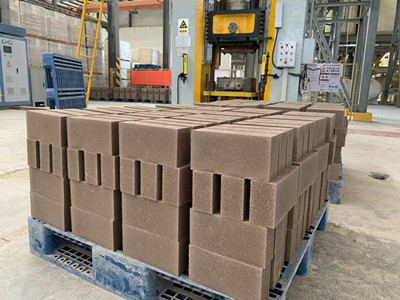
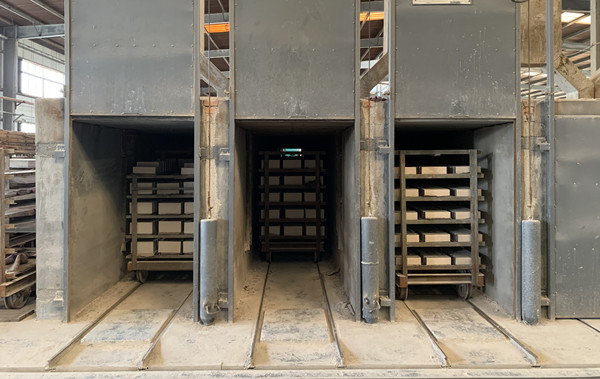
1. Refractoriness of Refractory materials
The property of refractory materials that can withstand high temperatures without melting under no load is called refractoriness. Refractoriness is a kind of technical index. For refractory materials, the meaning of refractoriness is different from the melting point. The most basic factor that determines the level of refractoriness is the chemical mineral compositions and distribution of the materials. Various impurity components, especially those with strong flux functions, will seriously reduce the refractoriness of refractory products. Therefore, the main way to improve the refractoriness of refractory materials in the process should be to take appropriate measures to ensure and improve the purity of raw materials.
Refractoriness is undoubtedly a technical index to judge the quality of refractory materials, the material no longer has mechanical strength and is not resistant to corrosion when it reaches this temperature. Therefore, it is not appropriate to think that the higher the refractoriness, the better the bricks. Only after considering other properties, we can comprehensively judge the value of refractory materials. Due to different applications, sometimes the refractory products with low refractoriness have a longer service life.
When refractory materials are subjected to high temperatures in use, they are usually accompanied by loads and fluxes of foreign objects. Therefore, the refractoriness of the product cannot be regarded as the upper limit of the product’s use temperature. Other properties must be comprehensively considered as a reference for the selection of refractory materials. In production, the purity of refractory materials can be relatively assessed through the refractoriness of raw materials.
The refractoriness data of some common refractory raw materials and refractory products are as follows:
Fireclay bricks 1610~1750℃
High alumina bricks >1770~2000℃
Magnesia bricks >2000℃
Sillca bricks 1690~1730℃
Dolomite bricks >2000℃
2, Refractories under load(RUL) of Refractory materials
The index of RUL of refractory materials at high temperature indicates its resistance to high temperature and load at the same time, and also indicates the softening range of refractory showing obvious plastic deformation.
The RUL is an important technical data of refractory materials because it indicates to a certain extent the structural strength of the product under conditions similar to its application. When refractory products are used on the supporting roof of a high-temperature kiln or as a pressure-bearing lining, especially when all sides are heated, if the material is heated to the level of softening and deformation, it will inevitably cause the kiln body to deform or even damage.
Increasing the purity of raw materials and reducing the content of low melting substances or fluxes will increase the RUL of refractories. This effect depends on their chemical composition, such as Na2O in fireclay bricks, Al2O3 in silica bricks, and SiO2, CaO in magnesia bricks are all harmful oxides, they will increase the amount of liquid phase and reduce its viscosity. On the other hand, adding certain additives to the ingredients in the brick-making process to improve the composition of the brick’s internal binding phase can increase the RUL of the product as well.
3, High-temperature volume stability of Refractory materials
When the refractory is used for a long time at high temperature, its shape and volume remain stable without change (shrinkage or expansion) is called high-temperature volume stability, which is an important technical index for evaluating refractory product quality.
During the firing process of refractories, the physical and chemical changes during the process generally do not reach the equilibrium state at the firing temperature. When the product is used for a long time and is subjected to high temperatures, some physical and chemical changes will still continue. On the other hand, in the actual firing process of the refractory product, due to various reasons, there are still have bricks with insufficient firing. For example, due to uneven temperature distribution in the same kiln, there will inevitably have products with insufficient firing. When this kind of product is used in the kiln under high temperature, some sintering changes continue, resulting in a change in the volume of the product—expansion or shrinkage. This irreversible volume change becomes a residual shrinkage or expansion, and also becomes a refiring shrinkage or expansion. The size of the re-heating volume change characterizes the high-temperature volume and stability of the product. So this index of refractory products has great significance for use. For example, for products built on the top of the furnace, if the re-fire shrinkage is too large, the bricks will fall off and cause the risk of damage to the overall structure. For other masonry structures, the joints of the masonry will also be cracked, reducing the integrity of the masonry and the ability to resist material erosion, thereby significantly increasing the damage of the masonry. In addition, this index can also be used to measure the degree of sintering of the product during the firing process. For products with bad sintering, the value of this index is bound to be larger.
4, Thermal shock stability of Refractory materials
Refractory materials are often subjected to rapid changes in high temperature during use. This destructive effect not only limits the heating and cooling speed of refractory products and kilns, but also limits the strengthening of kiln operation, and it is one of the main reasons for the rapid damage of refractory products and kilns.
The ability of refractory materials to resist sudden changes in temperature without being damaged is called thermal shock stability. This performance is also called thermal shock resistance or temperature sudden change resistance. Silica bricks are easy to generate cracks when exposed to rapid heat and cold. Magnesia bricks are easy to generate spalling, these bricks are usually referred to as materials with low thermal shock stability or low thermal shock resistance. On the contrary, it is a material with high thermal shock stability or high thermal shock resistance.
5, Slag resistance of Refractory materials
The ability of refractory materials to resist slag erosion at high temperatures without damage is called slag resistance. The concept of slag here, in a broad sense, refers to slag, fuel ash, fly ash, various materials (solid and liquid materials, such as sintered cement blocks, molten glass, etc.), and gaseous substances( Gas, carbon monoxide, etc.) that come into contact with refractory materials at high temperatures.
Slag erosion is the most common form of damage to refractories during use. The damage to the wall of the glass kiln and the lining of the cement rotary kiln is mostly caused by this effect. In actual use, about 50% of the damage is due to slag erosion, so it is very important to study the slag resistance of refractory materials.
The slag resistance of refractory materials is mainly related to the chemical mineral composition and organizational structure of the refractory materials and is also related to the nature of the slag and the conditions of its interaction. From the point of view of the production process, to improve the slag resistance of refractory materials, mainly from the following two ways:
1. Ensure and improve the purity of raw materials and improve the chemical mineral composition of products.
2. Select the appropriate production method to ensure the produced bricks have dense and uniform structure.