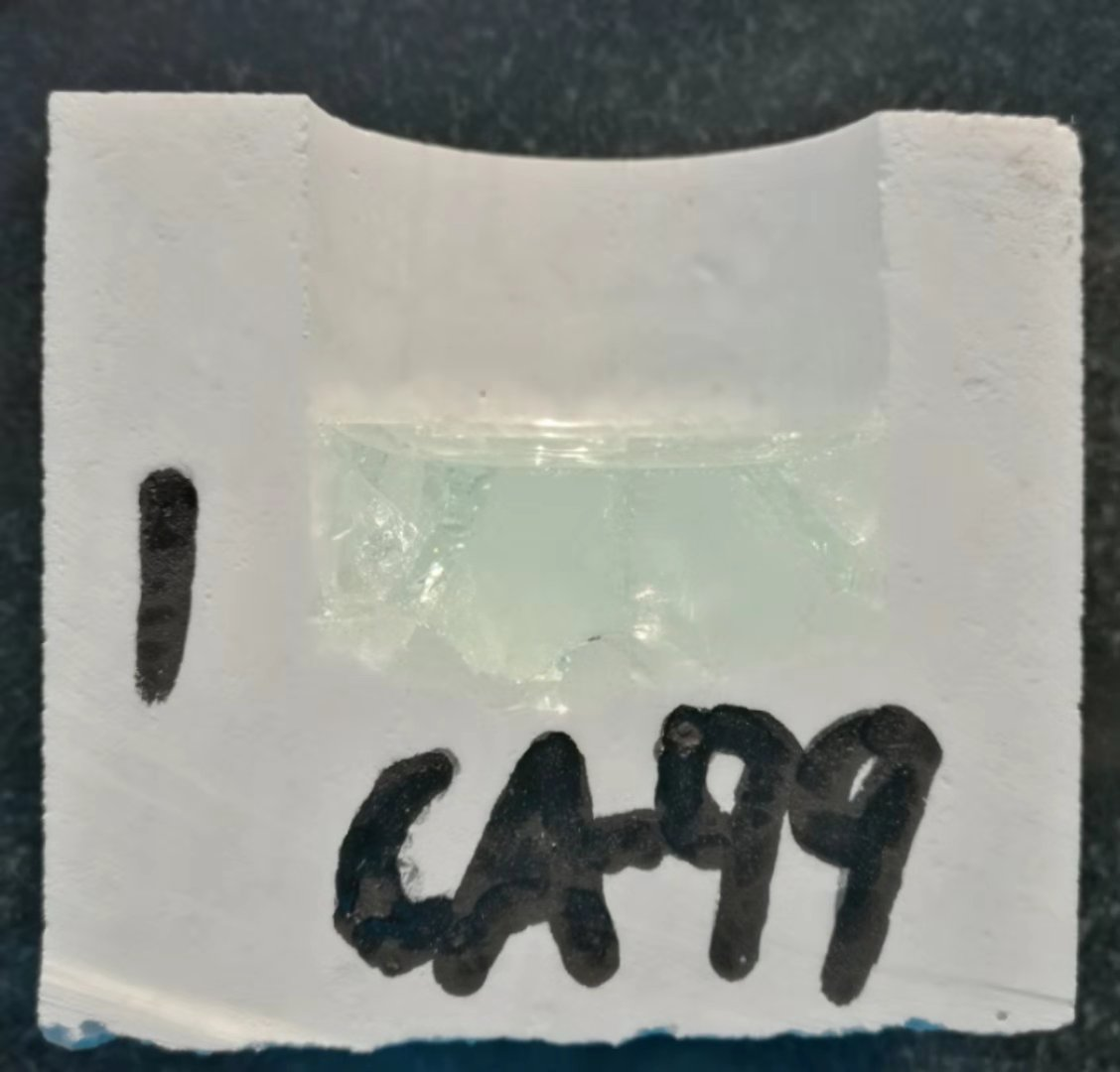
The basic introductions for Sintered dense-alumina feeder bricks ( CA -99 )
1, The properties of ( CA-99 ):
- High purity: reduce reaction corrosion
- Great compactness: reduce penetration and erosion
- Excellent corrosion resistance to glass liquid: does not cause defects to the glass
2, What raw material do you use for this product? ( the selection of raw material ):
We use high-purity sintered alumina as the main raw material and hydrated alumina as the binder for this product. its main chemical composition is Al2O3.
3, How do you manufacture this product? ( the production process )
–-The dosing and forming process
Since the forehearth refractory bricks are all large-sized refractory products, we use a special dosing method to make sure the stability of the products, and use a vibrating casting production method to ensure the quality of the bricks.
–The sintering process
Due to the high purity of the raw materials used, they must be sintered at a specific high temperature to achieve good sinterability.
The microanalysis for Sintered dense – alumina feeder bricks ( CA-99 )
1, Particle Scanning SEM:
The above is a picture of the aggregates observed under a scanning electron microscope after the sintered-dense alumina refractory bricks have been fired at a certain high temperature.
This aggregate photo was scanned after being magnified 1000 times. It can be seen from the picture that the sintered corundum we used is irregular and polygonal corundum polycrystals. The particle size of a single crystal is large, mostly around 30-50μm, and there is no glass phase in the middle, they are closely arranged, have low porosity, good bulk density, and can resist glass liquid erosion perfectly.
2, Matrix scanning SEM
Matrix material SEM scanning picture description:
The picture above is a scanning electron microscope picture of the matrix material after being magnified 5000 times. Because we used different particle sizes and different types of sintered alumina for the matrix ingredients. After high-temperature sintering, there is no glass phase, and the corundum grains show irregular and polygonal crystals, but the crystal grains are relatively small, mostly between 2-8μm, but they are very tightly interlaced and combined, which effectively prevents the glass liquid corrosion from the matrix part.
3, Diffraction analysis chart XRD:
The above figure is the XRD pattern of the sintered dense α-Al2O3 refractory bricks, the main crystal phase is α-Al2O3 phase. Because there is a small amount of Na2O and a very small amount of β-Al2O3, It also double ensures the product has excellent corrosion resistance because of these two materials.
Physical and chemical tests for Sintered dense – alumina feeder bricks ( CA-99 ) :
1, In order to get the physical and chemical properties of these sintered refractory products and the uniformity of materials, we took samples from different parts( bottom and side area )of the forehearth and made testings.
Below is the test result for the test we made:
Below are the test reports that we sent the samples to the third party:
From the test results, we can see that the sintered dense refractory materials in different areas of the feeder are uniform, with very high Al2O3 content, fewer impurities, low apparent porosity, good bulk density, high crush strength, and high temperature performance.
2, Glass erosion test:
We use the crucible method to cut the sintered refractory product into 80cm3 squares, drill a hole with a diameter of 43mm and a depth of 45mm, and put 65g of broken white glass materials into it. The composition of the broken glass material is as follows:
Since the temperature of the forehearth is generally 1200℃-1280℃, so we measured and calculated the 24h erosion rate at the junction of the three phases after holding at a temperature of 1350℃ for 72h.
Picture 1:
Picture 2:
glass erosion test result:
From the above test results, we can see that the corrosion rate is very slow because of the high purity and compactness of the sintered-dense refractory block, and there are no impurities in the glass, and as time goes by, the dissolved alumina in the glass at the interface increased, and alumina ( in the glass ingredients ) can reduce the tendency of glass crystallization and increase the viscosity of the glass liquid, thereby reducing the liquid glass erosion to the forehearth. The erosion will be slower and slower in the later stage of using and the performance will be better. These good performances of the CA-99 sintered refractory feeder brick have also been verified by our customers.
Below is a photo of our CA-99 sintered refractory product after 5 years of use:
Conclusion:
The sintered dense α-Al2O3 forehearth refractory brick made with sintered alumina as the main raw material has excellent properties such as high purity, good compactness, and excellent resistance to molten glass; it can prevent the generation of glass defects and is the ideal fire-resistant refractory brick for the forehearth of the glass industry, like the bottle glass furnace, and container glass melter furnace.